Beam Engine
Today's Mural by Jim Corsiter
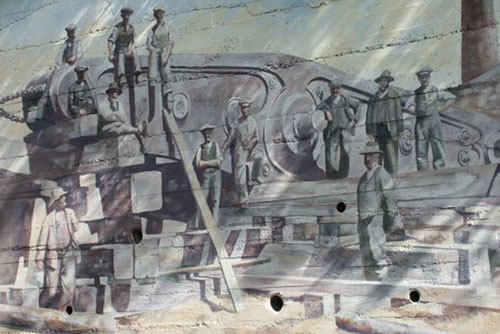
The Engine
The engine was manufactured by Messrs. Harvey & Co., of Hayle,
Cornwall, in 1874. The parts were shipped from Corn- wall to Morison's
Haven harbour, adjacent to the colliery, and It is assumed that
the engine beam, weighing approximately 30 tons, was raised into
position in stages by means of jacks, as the building of the engine
house progressed. The Beam is 33 ft. long and 6 ft. 4 ins. deep
at the centre. The fulcrum is 18 ft. from the steam end. The cylinder
is 70" diameter x 12'0" stroke. The trunnion is located off centre,
giving the pump rams a stroke of 10'0". The normal speed of the
engine is 3Vs strokes per minute and the pumping capacity was
650 gallons of water per minute allowing an efficiency of 70%.
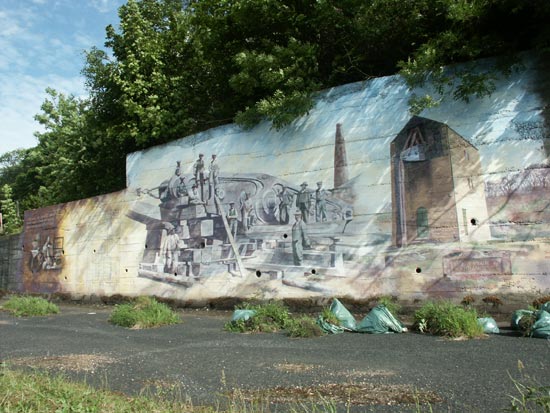
The Engine still stands for the 21st Century
Valve Mechanism
The engine is fitted with three operating valves of the double
beat balanced type (Cornish Valves) opened by means of dead weights,
levers and trip rods actuated by the release of detents and controlled
by cataracts situated below floor level. The cataracts are simply
water tanks containing floats attached to the detent trip rods
and the operation of the valves is controll- ed and timed by regulating
the size of opening through which the water from the tank is released.
The valves are closed by means of adjustable tappets attached
to the plug rod suspend- ed from the engine beam. The three main
valves for controll- ing the engine are the steam valve for admitting
steam to the top of the piston, the exhaust valve for releasing
the steam on the bottom side of the piston to the condenser during
the downstroke and the equilibrium valve which is opened at the
end of the downstroke, allowing steam to flow from the top to
the bottom of the piston during the upstroke. A water in- jection
valve is also fitted to admit water to the condenser at the end
of the upstroke when the exhaust valve opens.
The Working Cycle
The working cycle of the engine for a complete stroke is as follows:-
Steam at boiler pressure is admitted to the top of the cylinder
viathe Steam valve, forcing the piston downwards and thus raising
the pumprods and rams. At the start of the downstroke, therefore,
the steam valve is open.the exhaust valve from the bottom of the
cylinder to the condenser is open and the equilibrium valve is
closed. At a predetermined point near the bottom of the stroke,
the steam valve closes and the downward stroke is completed by
the expansion of the steam in the cylinder. When the piston has
reached the bottom of the stroke, the equilibrium valve opens
and the ex- haust valve closes, allowing the steam to flow from
the top side of the piston to the bottom side. Both sides of the
piston are now in a state of equilibrium and the dead weight of
the pumprods and rams starts the pumping stroke, causing the piston
to travel upwards. Shortly before the piston reaches the top of
the stroke, the equilibrium valve closes and the piston is brought
gently to rest due to compression of the steam re- maining in
the top part of the cylinder. The exhaust valve now opens, also
the injection valve to the condenser, thus creating a vacuum in
the cylinder below the piston. The steam valve then opens and
the cycle is repeated.
Reconstruction
Some years after Prestongrange Colliery was taken over by the
Summerlee Iron Company in 1895, it became necessary to in- crease
the capacity of the shaft pumps and It was decided to install
28" diameter rams. The main pumps consist of two 28" force pumps,
one at the Great Seam level, and one about midway between thatand
the surface, raising the water in two stages. At the Beggar Level,
below the Great Seam, is another pump 17" diameter, which pumps
to the Great Seam lodge- ment. The pump rods, of Oregon pine,
are 23" square from the surface to the top lift pump and the total
weight of the pump rods, rams, crossheads and side rods is about
105 tons. Calculations of the engine beam strength showed that
the beam as it stood was not capable of bearing the extra load
im- posed by the installation of the larger pumps, consequently
a strengthening truss was designed. Fitting of this truss was
no mean feat, bearing in mind that, at that time, no electrical
power was available for drilling machines.etc. A specially con-
structed boring bar, driven by a small steam engine was used for
drilling the large holes in the sides of the beam to receive the
pins in the eyes of the tiebars. When the truss had been erected,
a system of levers was fitted to the beam for the pur- pose of
measuring the deflection to ensure that the beam was not unduly
stressed when tightening the tie bars.
Mishaps To Cylinder
About 1916, a serious mishap occurred due to the fracture of the
piston rod when the piston was at the top of the stroke. The impact
caused by the falling piston broke the cylinder bottom and cracked
the cylinder wall. A new cylinder bottom was cast and it was decided
to attempt to repair the cylinder by clamping. Heavy cast iron
rings were made in halves and these were bolted together round
the cylinder. The cracks were caulked with a mixture of red lead
and boiled linseed oil, after which the set-screws round the rings
were tightened to close the cracks. No further trouble was experienced
until 1938 when the piston rod again broke under the same condi-
tions. Another cylinder bottom was fitted and the repair of the
walls was achieved by removing the clamping rings and cutting
dovetailed grooves inserting and clamping up strips of soft copper.
The engine continued working until pumping by means of the Cornish
Pump finally ceased in 1954.
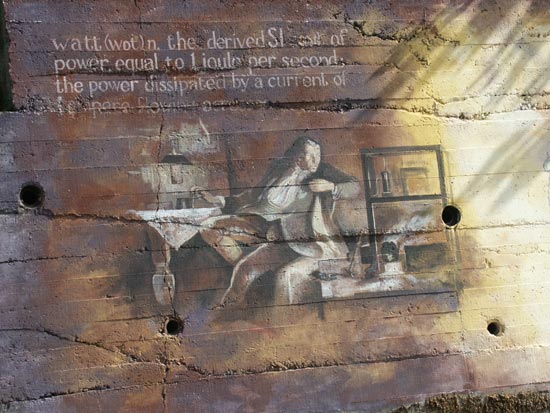
The Historical Site
The Beam Engine, now an Industrial Monument, is the centre-piece
of a Historical Site for the Mining Industry. The first written
record of coal mining in Britain Is the Charter given to the monks
of Newbattle in 1210 to work the coal in the Grange of Preston.
The first coal 'harbour, Acheson's Haven, lay across the road
and the first railway in Scotland was laid on wooden rails from
Tranent to Cockenzie, some three miles down the coast.
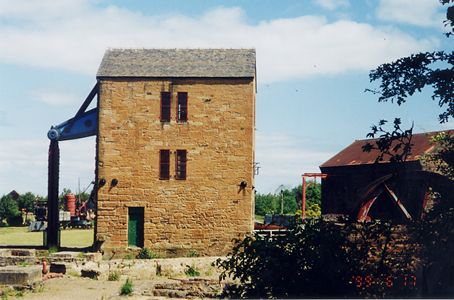
These and other noticeable landmarks are accessible today via
The Coal Trail.
|